Capabilities Of Transparent FPC
ITEM | UNIT | CAPABILITY | |
Limit Tolerance | Normal tolerance | ||
Layer | / | 1-6 layer | 1-6 layer |
Cutting size | mm | 250*1000mm | 250*500mm |
Min. thickness | mm | 0.075mm | 0.10mm |
Adhesive stiffener | um | PSA:50um | PSA:50um |
Hot setting adhesive | um | 12.5/25/40um | 12.5/25/40um |
Min. drilling hole size | mm | 0.1 | 0.2 |
Hole diameter tolerance | mm | ±0.075 | ±0.1 |
Hole wall copper thickness | um | 8/15/25 | 8/15/25 |
Min line width/space | mm | 0.05/0.05 | 0.075/0.075 |
Line width tolerance | mm | ±0.03 | ±0.04 |
Silk screen thickness | um | 8 | 15 |
Immersion gold | um | Ni: 2.0~5.0 | Ni: 2.0~5.0 |
Au: 0.03~0.08 | Au: 0.03~0.08 |
Base Material
Transparent FPCs are typically made from flexible and transparent substrates. One common material used for transparent FPCs is a type of flexible plastic film, such as polyethylene terephthalate (PET) or polyimide (PI). These materials offer transparency and flexibility, which are crucial for applications where you need to bend or conform the circuit to non-planar surfaces while maintaining see-through properties.
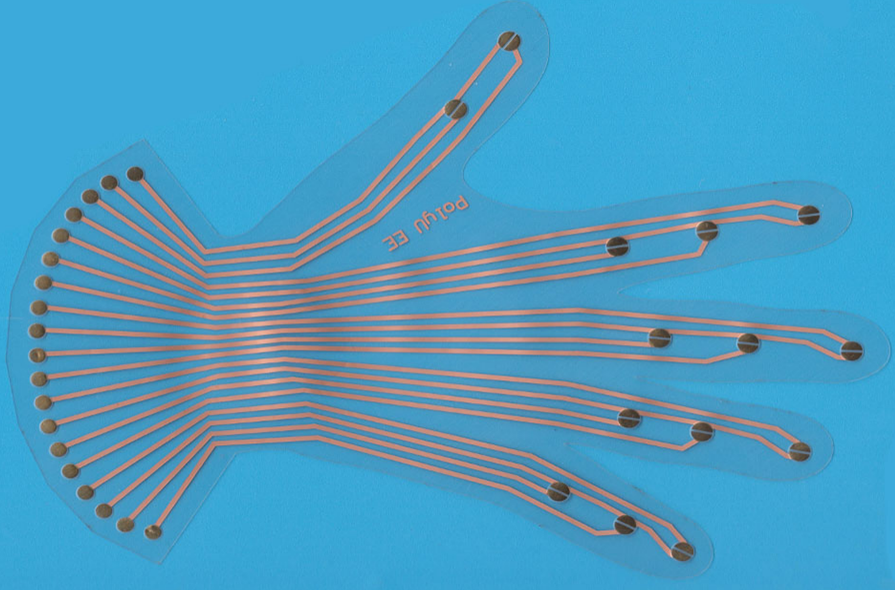
The stack-up of a transparent FPC can vary depending on the specific requirements of the application. A basic stack-up might include the following layers.
a. Transparent Substrate This is the base layer, usually made of PET or PI, which provides flexibility and transparency.
b. Copper Traces These are the conductive traces that carry electrical signals.
c. Insulation Layer A dielectric layer that insulates the conductive traces from each other.
d. Cover Layer A protective layer that can also enhance transparency and provide durability.
e. Solder Mask (optional) If surface mount components are used, a solder mask layer may be applied to protect the exposed copper traces.
The specific stack-up and materials can be customized to meet the needs of the application, and more complex multi-layer designs are also possible to accommodate intricate circuitry.
Manufacturing Process
The manufacturing process of transparent FPCs is similar to that of traditional flexible PCBs, with some modifications to ensure transparency. It involves several key steps.
a. Material Preparation The transparent flexible substrate material is prepared, usually in the form of a roll or sheet.
b. Circuit Design The circuit pattern and electrical traces are designed using specialized software like .
c. Printing The circuit pattern is printed onto the substrate using techniques such as screen printing or inkjet printing.
d. Etching Unwanted copper or other conductive material is etched away to form the desired circuit pattern.
e. Component Attachment Surface mount components can be added to the transparent FPC.
f. Lamination Multiple layers can be laminated together to create a multi-layer FPC.
g. Testing The FPC is tested for electrical continuity and functionality.
h. Cutting and Shaping The FPC is cut and shaped to the desired dimensions.
i. Finishing Any necessary finishing steps, like the application of protective coatings, are performed.
Applications
Transparent FPCs are used in various applications, including but not limited to:
a. Consumer Electronics Transparent FPCs can be found in devices like smartphones, tablets, and wearables to connect and route components while maintaining aesthetics and form factor.
b. Automotive they are used in automotive displays and infotainment systems where transparency is required for heads-up displays and touchscreen applications.
c. Medical Devices Transparent FPCs are used in medical equipment, such as endoscopes and ultrasound machines.
d. Wearable Technology In products like smart glasses and fitness trackers.
e. Aerospace Transparent FPCs can be used in aircraft displays and lighting systems.
f. Industrial Control Systems In applications where flexibility and transparency are needed for control panels and instrumentation.
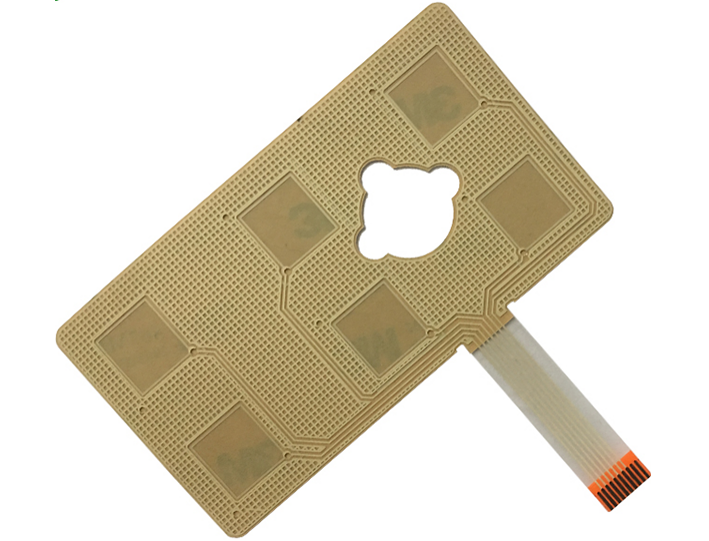
Transparent FPCs offer unique advantages in applications where aesthetics and flexibility are crucial, while still maintaining reliable electrical performance.