Capabilities Of FPC Assembly
ITEM | UNIT | CAPABILITY | |
Limit Tolerance | Normal tolerance | ||
Layer | / | 1-6 layer | 1-6 layer |
Cutting size | mm | 250*1000mm | 250*500mm |
Min. thickness | mm | 0.075mm | 0.10mm |
Adhesive stiffener | um | PSA:50um | PSA:50um |
Hot setting adhesive | um | 12.5/25/40um | 12.5/25/40um |
Min. drilling hole size | mm | 0.1 | 0.2 |
Hole diameter tolerance | mm | ±0.075 | ±0.1 |
Hole wall copper thickness | um | 8/15/25 | 8/15/25 |
Min line width/space | mm | 0.05/0.05 | 0.075/0.075 |
Line width tolerance | mm | ±0.03 | ±0.04 |
Distance between hole edge to outline | mm | ≥0.4 | ≥0.5 |
Solder mask thickness | um | 8 | 15 |
Silk screen thickness | um | 8 | 15 |
Immersion gold | um | Ni: 2.0~5.0 | Ni: 2.0~5.0 |
Au: 0.03~0.08 | Au: 0.03~0.08 |
Key Points of FPC SMT Process
Abstract: With the trend towards miniaturization in consumer electronic products, the application of Flexible Printed Circuits (FPC) is becoming increasingly widespread.
The SMT (Surface Mount Technology) process for FPC differs from traditional PCBs, and this article provides a detailed description of the key process steps in FPC SMT production, including pre-treatment, fixation, printing, component placement, reflow soldering, testing, inspection, and separation.
This information will be helpful for readers who are new to FPC SMT production.
Keywords: FPC, SMT, FPCA,Flexible PCB SMD,FPCA,FPC assembly.
A PCB (Printed Circuit Board) is a rigid board used in electronics.
FPC (Flexible Printed Circuit), also known as a flexible circuit board or flex board, is a flexible circuit board.
It is commonly referred to as a flexible board. Miniaturization of electronic products is an inevitable trend in development.
For many consumer products, surface mount components (SMD) are assembled on FPC due to space constraints, facilitating the overall assembly of the device.
FPC has found widespread application in digital products such as calculators, smartphones, digital cameras, and camcorders.
Conducting SMD surface mount assembly on FPC has become one of the trends in SMT (Surface Mount Technology) development.
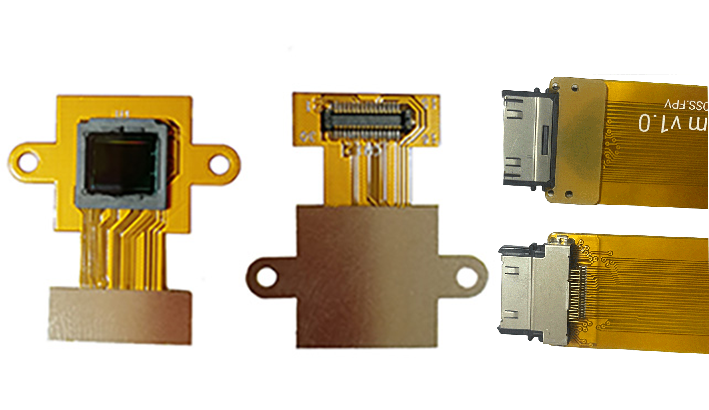
The SMT (Surface Mount Technology) process requirements for FPC (Flexible Printed Circuit) differ significantly from traditional rigid PCB (Printed Circuit Board) SMT solutions. To achieve success in the FPC SMT process, proper positioning is of utmost importance. Due to the inherent flexibility and softness of FPC boards, it's essential to use dedicated carriers or fixtures. Without them, it's impossible to secure and transport the FPC boards, which are fundamental for processes like printing, component placement, and reflow soldering in SMT. The following are detailed descriptions of key process steps in FPC SMT production, including pre-treatment, fixation, printing, component placement, reflow soldering, testing, inspection, and separation:
Pre-treatment:
Before SMT, FPCs may undergo surface cleaning and preparation to ensure proper adhesion and solderability of components.
Fixation:
To overcome the flexibility of FPCs, specialized carriers or fixtures are used to securely hold and transport the boards during the SMT process.
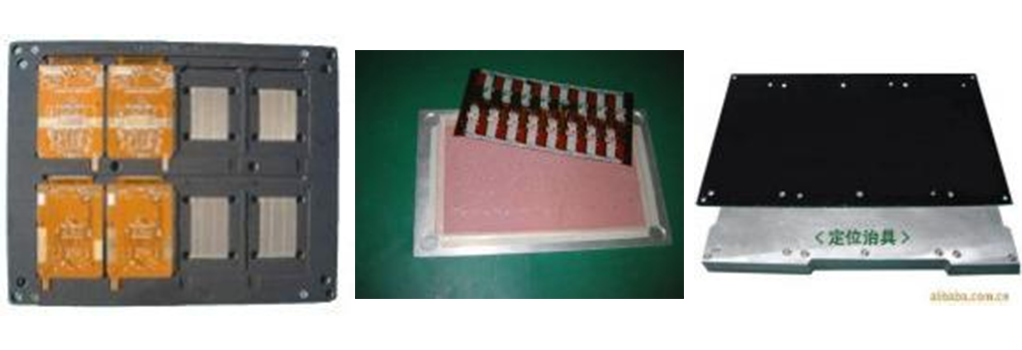
Printing:
The solder paste is accurately applied to the FPC's pads using a stencil or screen-printing process, ensuring precise component placement.
Component Placement:
Surface mount components (SMD) are carefully placed onto the FPC, aligning them with the solder paste on the pads.
Reflow Soldering:
The FPC with components is passed through a reflow oven, where the solder paste is melted to form strong electrical connections between components and the FPC.
Testing:
Functional and electrical testing may be performed to verify the integrity of the solder joints and the overall functionality of the assembled FPC.
Inspection:
Visual inspection and quality control measures are carried out to identify any defects or issues that may require correction.
Separation:
After completing the SMT process, the FPCs may be separated from their carriers or panels, getting them ready for further assembly or integration into electronic devices.
In summary, the unique characteristics of FPCs, such as their flexibility, necessitate special handling and fixation during SMT. This is critical for ensuring precise soldering and the overall quality of the assembled components. Properly addressing these differences is essential for successful FPC SMT production.