Capabilities Of Double layer FPC
Item | Finished Cu Thickness | Min.Trace Width | Min.Trace Spacing(mil) |
Circuit | 12-18um | 2mil | 2mil |
18-35um | 3mil | 3mil | |
35-50um | 4mil | 4mil | |
50-70um | 6mil | 6mil | |
Surface Treatment | Thickness | ||
OSP | / | ||
(HASL) only for rigid flexible PCB | Sn: 2um-40um | ||
(HASL L/F) only for rigid flexible PCB | Sn: 2um-40um | ||
ENEPIG | Ni: 1.0um-6.0um Pd: 0.10um Au: 0.10um | ||
Hard gold plating | Ni: 1.0um-6.0um Au:0.02um-2um | ||
Soft gold plating | Ni: 1.0um-6.0um Au:0.02um-1um | ||
ENIG | Ni: 120-200U” Au: 2-4U” | ||
Immersion silver | Ag: ≥0.4um | ||
Tin plating | 2um-15um |
Structure
A double-layer FPC typically consists of the following key elements:
a. Raw material: The base material usually made of flexible materials like polyimide (PI) or polyethylene terephthalate (PET), which provides the FPC with its flexibility.
b. Conductive Layers: Two layers of copper or other conductive materials are bonded to the base material. These layers serve as the conductive lines for electrical signals.
c. Insulating Layer: An insulating layer or dielectric material is placed between the two conductive layers to prevent electrical short circuits and provide mechanical support.
Advantages
Double-layer FPCs offer several advantages:
a. Enhanced Circuit Density: With two conductive layers, designers can create more complex and denser circuit patterns, which can be crucial in applications with space constraints.
b. Improved Signal Integrity: Double-layer FPCs can effectively route and shield signals, minimizing crosstalk and interference between adjacent traces.
c. Design Flexibility: The dual layers allow for different routing configurations, including interconnections and the ability to accommodate both surface mount and through-hole components.
d. Reliability: The insulating layer between the conductive layers ensures reliable electrical isolation and prevents short circuits.
Manufacturing Process
The manufacturing process of double-layer FPCs is similar to that of single-layer FPCs with an additional layer of copper and insulation. It involves steps such as material preparation, drilling holes, copper etching, lamination, shape and testing. The key difference is in the careful alignment and bonding of the two conductive layers with the insulating layer sandwiched in between.
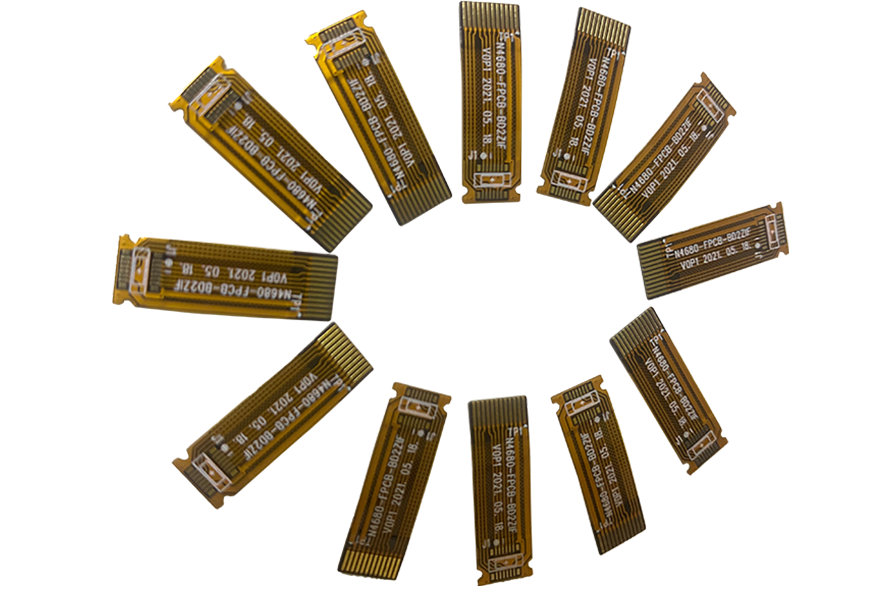
Applications
Double-layer flexible circuits are used in various industries and applications, including:
a. Consumer Electronics: They are found in smartphones, laptops, cameras, and other portable devices to accommodate complex interconnections and slim designs.
b. Automotive: Double-layer FPCs are used in vehicle infotainment systems, dashboard displays, sensors, and control modules.
c. Medical Devices: In applications like medical imaging equipment, patient monitoring devices, and diagnostic instruments.
d. Aerospace and Defense: Used in avionics, radar systems, and communication devices.
e. Industrial Equipment: Double-layer FPCs can be found in control systems, industrial automation, and robotics.
f. Telecommunications: They are used in network infrastructure, routers, and communication equipment.
Design Considerations
Designing a double-layer FPC requires careful consideration of factors such as the stack-up, routing, and material selection to ensure that the circuit functions reliably and can be manufactured effectively. Designers must also consider the flexibility and bending requirements of the FPC, as well as thermal and environmental conditions in the application.
Double-layer FPCs are an excellent choice when more complex circuitry and a higher level of interconnectivity are needed in a flexible and space-efficient package. Their use is widespread in industries where compact and reliable flexible circuit solutions are required.